Interview
転舵した芸術系人間が生み出したのは、現場にも設計にも寄り過ぎない搬送機構。
機械系エンジニア
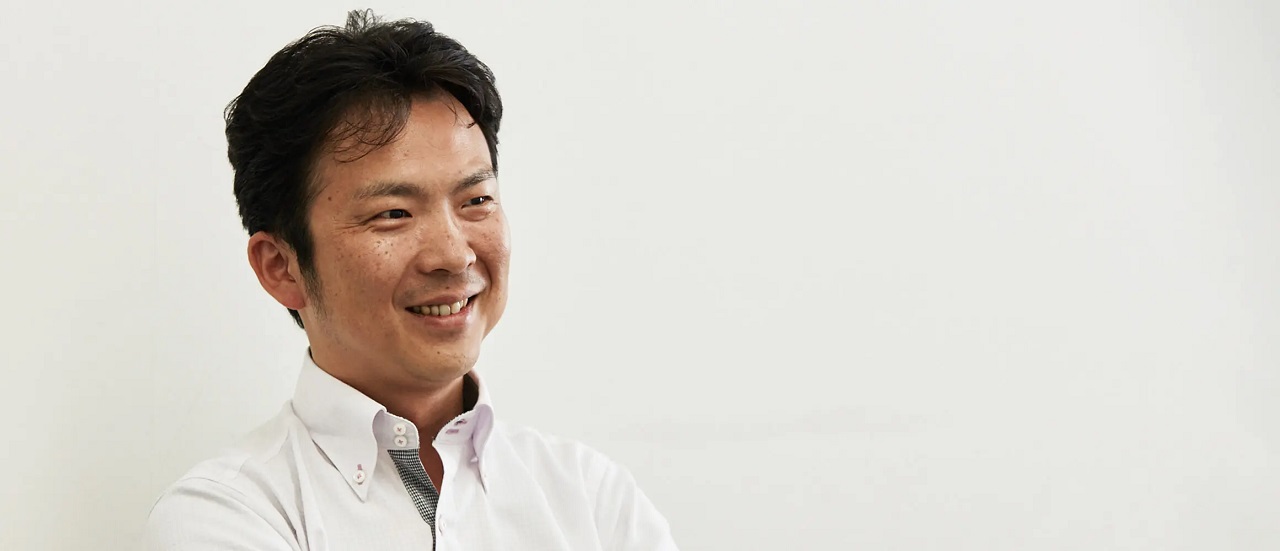
エンジニア略歴
- 1998年新卒入社
- 1998年~自動車部品鋳造型ライン導入準備
- 2000年~フラットパネルディスプレイ製造装置の調整・加工・組立、技術管理
- 2006年~フラットパネルディスプレイ製造装置内搬送系機構の設計・開発
「ものづくりにかかわりたい」一心で、
芸術系から方向転換。
得意科目は体育と図画工作。機械いじりも大好きで、将来の夢は「大工さん」。おまけに家業が印刷会社であれば、自然に理系の道を選びそうだが、吹田さんは違った。
「芸術系大学に進みました。絵を描いて生活できるイラストレーターに魅かれていたのです。でもすぐに、自分と同じレベルのデッサン力を持った人がたくさんいることに気付き、方向転換(笑)。一方で自分の手でものをつくり出したい思いも強く、家具やインテリアを学ぶインダストリアルデザイン学科を選びました。最終的には同じインテリアでも、ライティングで空間の効果を演出する照明デザインにのめり込んでいきました」
同時期、近所のバイク店に集まる仲間と誘い合い、バイクや車を分解しては組み立て直す、機械いじりの情熱も再燃した。チューンナップしたバイクで、レースにも参戦していたというが、やがて就職シーズンを迎える。
「友人たちが次々に内定を決めるのを目にしながら、これまで学んできた分野で就職するのが無難だろうとは考えていました。ただ、ものづくりに対する思いも捨て切れず、揺れる日々でした」
悩んでいたころ、さまざまな分野の世界に自由に飛び込んでいけそうなメイテックを偶然知り「やってダメならまた方向転換すればいい」と入社を決める。技術的知識はもちろん皆無。「君のような経歴は珍しい。おもしろいからぜひ来なさい」という面接官の言葉を信じ、決意した。
学んだことや得意な絵、好きな機械いじりが仕事に活きることは、ほどなく実感する。
現場に一歩も二歩も入り込み、
気付きを提案して、居場所をつくる。

入社後、最初の配属先は自動車メーカーの製造工場。生産技術部門の部品鋳造工程の整備業務で「正真正銘」のものづくりの現場だった。
「工場内のシリンダーヘッド鋳造型ラインに一日中張り付き、現場での生産不良率を0% にして作業効率を高めるのが目標でした。誰がつくっても不良のない鋳物(いもの)にするため、金型に溶かしたアルミを注ぐ時間、空洞部をつくるための中子を入れる時間、型の温度・温度分布などなど、車種ごとに何十通りもある項目を計測・集計する。同時に、新車種が出たら、型に切れ目を入れてみたり、中子が中で割れたりしないよう型を変えてみたりと、精妙に絡まりあった項目の一つを変え、そのデータをひたすら取っていきました」
現場に身体がなじんできたころ、機械いじりの延長か「ここをこうすれば」と気付く機会が多くなった吹田さんは、一歩も二歩も現場に踏み込んで、体験したことを提案の形でぶつけてみた。セキュリティや情報の管理が徹底された工場だったが、現場の人たちは吹田さんの意見に耳を傾けてくれたという。間もなく見えてきた風景がある。
「どんどん自分の場所がつくられていくのが分かったんです。指示を待つのではなく、自分が経験したプラスアルファを提案するから説得力を持ち、コミュニケーションも深まる。そこに思いが至り、現場が一層好きになりました」
その意味では、最初の経験が「設計」ではなかったことが逆に幸いしたと笑う。今も変わらない、仕事に向き合うスタイルがこの時点で萌芽(ほうが)したのだから、と。そしてスタイルは、次の配属先で身に付いていく。
再びの「現場」。装置の不具合対策を
二次元CADでラフにし、多方面に提案。
「現在も在籍している大手光学器メーカーのフラットパネルディスプレイ(以下、FPD)製造装置部門への配属ですが、当初の6年間は装置製造の調整・組み立て部門でした」
吹田さんは、FPD 製造装置内のガラスやプレートなどを搬送するロボット全般の調整に携わることになる。当時第二世代と呼ばれた装置は、世界に一台という触れ込みだったが、吹田さんの配属前、調整に難航しており、解体されていた。その反省を受けて開発されたという、画面の小さなステッパー型から進化した初めてのスキャン型装置は、まだまだ開発途上の段階だった。
「完全新規の装置だったので、各所に改善の余地があり、調整してもリカバリーができない不具合が頻発しました。目先の開発に一杯の設計に業を煮やし、自分で工程を思い描き、二次元CAD を使って描き変えた変更点のラフを設計に持ち込んでは提案し、必要な治具は生産技術と話をつける。実際にものを扱っているぶん、注文は具体的で説得力があります。自分なりの提案を持っては、あちこちにアプローチして、そのやりとり自体も楽しんでいました」
デッサンや塑像(そぞう)の素養が活きたのか、二次元CAD の立体化作業は頭の中で自然にできたという。やがて次世代装置の開発のため「経験者の声が欲しい」という声が社内で聞こえてきた。信頼してくれていた設計部門の課長に就業部署の異動ができないかを打診してみると「ぜひ来い」。お客さま内ローテーションが実現した。
やりがいのある仕事に出会えたのだから、
プラスアルファの提案をし続ける。
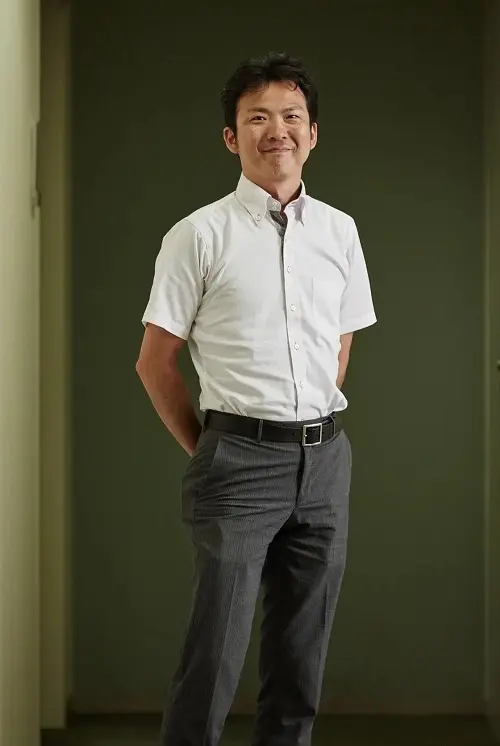
「担当は搬送系機構の新規開発にかかわる、全体構想計画と仕様設計でした。それまでの経験や知識が活かせ、ほぼ成熟した装置とはいうものの、さらなる効率性と安全性の向上、低コストの実現は至上命題です。好きに文句を言ってきた手前、ヘタなものはつくれないプレッシャーがある。調整や組み立て部門が何を求めているかを関連部署と徹底的にコミュニケーションし、議論を重ねました」
試行錯誤を繰り返し、現場とは異なる充実感を味わった果てに、提案は製品の機構に結実し、その過程で複数の特許も取得できた。続いて新機種開発を手掛ける。
「製造時代に見慣れたマスクサイズだったため『何をしてもいい』と任されても戸惑いはありませんでした」。やりたいことがすぐ明確になり、高精度で余分が削ぎ落とされた、満足のいく製品が生み出せた。「シンプルなのに完成形」を追求し提案する過程で、現場にも設計にも寄り過ぎない、仕様書にもとらわれない「ものづくりの流れを組み立てられる」自分なりの設計が、見えてきたという。
「FPD 部門は業績が好調なので開発予算もあり、提案を受け入れられる余地が大きい。しかも設計に留まらず、計画立案から製作工程、完成した装置に実際に触れる環境も与えられています。好循環にあるお客さまに恵まれ、せっかくやりがいある仕事に就けたのですから、指示待ちで動くのではなく、やはりお客さま先に入り込んで楽しみながら、プラスアルファの提案をすることをこれからも心掛けたいですね」
だから次の開発も「核心を違えず、自分勝手に走らず、解答はブレず」と胸に刻んでいる。
※当社社内報「SYORYU」:2016年秋発刊号に掲載した記事です