Interview
エンジンから、機構、外装、解析へ。
美しくつくりやすい、人を幸せにするパズルへの挑戦。
機械系 生涯プロエンジニア(R)
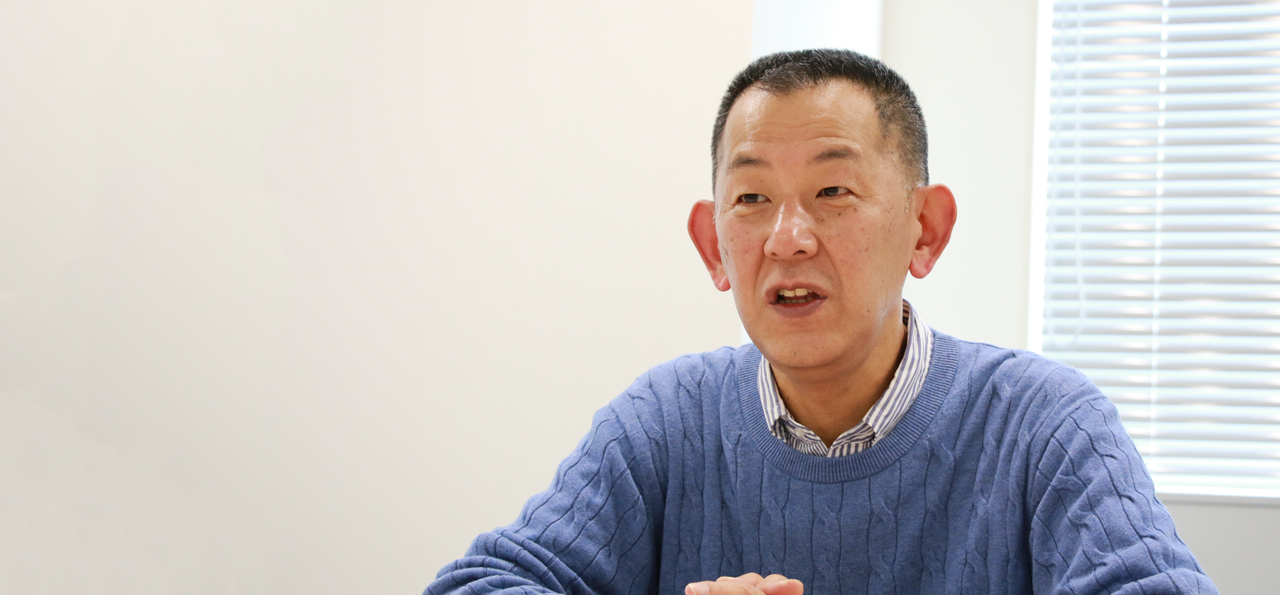
エンジニア略歴
- 1987年メイテック新卒入社
- 1987年~自動車燃料系部品の設計
- 1991年~自動車用ガソリン機関の設計
- 1992年~自動車用ディーゼル機関の設計
- 1993年~大型車両駆動・操舵装置部品の設計
- 1995年~磁気ディスク装置の設計
- 1995年~医療用画像診断装置の設計
- 1996年~デジタルビデオカメラの設計
- 1998年~フィルムスキャナーの設計
- 2000年~DVDプレーヤーの設計
- 2005年~インクジェットプリンターの設計
- 2019年~ガラス製品製造装置の設計・製造管理
- 2023年~次世代エネルギー燃焼装置開発
- 2024年3月定年到達
バイク好きが高じて
可能性を求めメイテックへ
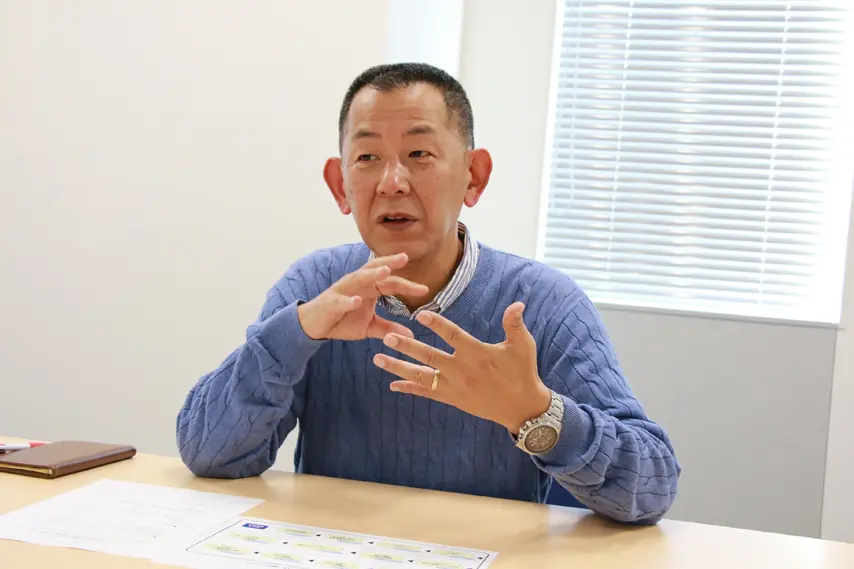
横浜で育って、子どもの頃はパズルやドリル好き。考えて、試行錯誤して答えを出すのが好きでした。それは進学先を考えたときに理数系を選ぶことにもつながり、地元の大学で機械工学を学びます。卒業研究は「ホブ切り歯車のシミュレーション」。ホブという工具を使って歯車の加工をするとき、直線が少しずつ変化していきます。精度を高めた形状で力を伝達できる最適な形状を求めて、当時のパソコンで簡単なプログラムを組んで分析しました。
学生時代の一番の思い出はなんといってもバイクです。高校生からチューンアップした愛車でサーキットを疾走することに夢中。レースにも出てテレビに映ったこともありました。それが高じて「二輪メーカーに入って製品づくりをしたい」と夢見ましたが、狭き門で希望はかないませんでした。せめて自動車に関わりたいと探していた時に、就職情報誌で見つけたメイテックの記事の中に「四輪・二輪の開発に関わる人もいる」という記載を見て、ここはどうか?と応募し入社することを決めました。
入社後は研修で図面の引き方をたたき込まれ、技能訓練センターで鈑金を切ったり、溶接したり、軸受けBOX をつくったりする実習も受けました。配属は遅いほうで、当時は配属への焦りを感じていましたが、加工や製造を視野に入れた設計の重要性を理解し、「あのとき加工を体験して良かった」と思うようになるのはまた後のお話です。
初配属で知識不足を痛感。
「つくり方」の重要性を知る
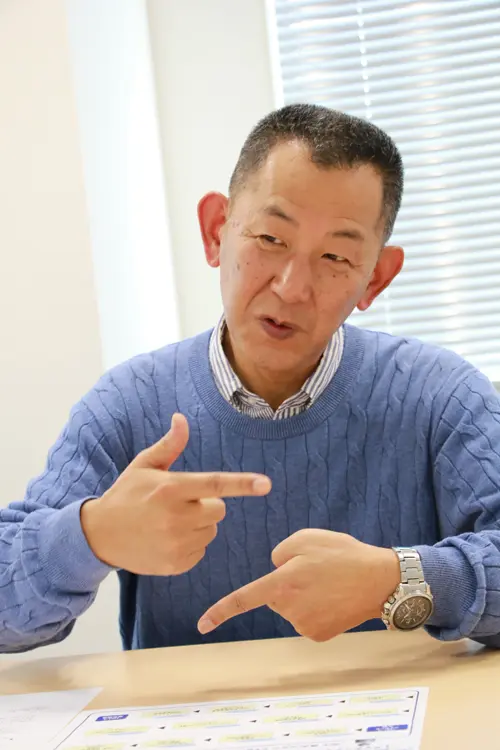
最初に配属されたのは、日本有数の自動車メーカー。燃料系、つまりエンジン部品の設計チームで、燃料レギュレーターやインジェクターなどの部品を設計する業務を担当しました。お客さまが即戦力のエンジニアを求めていたのに対し、新卒で配属された私の技術は周囲と比べ劣っていました。配属直後にはエンジンの構造や製造工程の理解不足から、加工できない部品を設計して「君にはもう頼まん!」と上司に言われてしまったことも。それが口惜しくて、負けたくなくて。結果を出そうと勉強を重ね、最後には部署を統括する社員の方に「君はうちの同年代のエンジニアよりできる」と言っていただけました。技術や会議体、仕事の分担など、仕事をする上で必要だと思えば遠慮なく言う性分で、それも含めて私を買っていただいたように思います。燃料系部品の設計業務は3年10カ月継続し、その後は系列の研究所やメーカーで軽量エンジンの研究開発やディーゼルエンジンの開発に関わりました。
次の配属では、別の自動車メーカーでトラックやバスなど大型自動車の駆動・操舵に関わるフレームやハンドル回り、サスペンションの設計に携わりました。1社目の業務はエンジン回りで、使用する金属が主に鋳物だったのに対し、今回使うのは鋼材です。ギアを使ってハンドルの回転を直線運動に変えて、機構でものを動かす設計はパズルのよう。考えるのが楽しかったですね。このお客さまは製造部門が近く、自動車関係では加工や製造の現場を一番見ることができました。サーキットテストにも参加し、「こういう風につくっているんだ」と実感。「机上の設計ではものづくりはできない、加工を知り、現場を知ることが大事だ」という考えは私の基礎となっています。
企画から製造まで
視野を広げた設計をさらに追求
1995年からは光学機器メーカーへ。通算で18年間契約が継続することになります。最初の業務は、医療用の画像診断装置の機構開発でした。それまで撮影フィルムを現像し利用していたレントゲンに、インクジェットプリンターの技術を取り入れるプロジェクト。樹脂シートに直接プリントすることで、時間をかけずに画像を確認できるというものです。構造はプリンターと同じですが、診断に影響するような影や汚れは厳禁です。また、エンジンを掛けたレントゲン車で装置を利用することがあり、その振動による画像の乱れも許されません。シビアな条件ですが、シートの送り方に工夫を加えるなどアイデアに富んだ製品づくりができました。
同じ会社で、デジタルビデオカメラの筐体設計にも関わりました。動画撮影をアナログからデジタルに転換する先駆けとなる製品。録画データを手のひらサイズのビデオカセットテープにデジタル信号として記録するものでした。デザイナーから素材やカラーにこだわった外装を求められ、複雑な接合が必要な箇所もありました。お金と手間をかければたいていのことは可能とはいえ、製品設計でそれはできません。コストを掛けずにどうやって形状や色を実現しようかと、これもまたパズルを解くように頭を悩ませる日々。つくりやすく、美しい製品を目指し、加工や製造、検査のしやすさまで視野に収めた設計を追求した仕事でした。
ここでの契約は2000年に一度終了し、別のエレクトロニクスメーカーで、DVDプレイヤーの開発に関わりました。面白かったのが300枚のディスクをプレイヤー内に収納し、選択・再生する機構を組み込んだ輸出用プレイヤー。円形の収納スペースを回転させて読み取る方式を採用しました。試作段階で300枚のディスクがドミノ倒しに、なんてこともありましたが、無事製品になりました。
このお客さまは、構想・設計・部品調達・生産立ち上げまで全てを任せてくれるところにやりがいがありました。生産の立ち上げのためマレーシアの工場に長期出張し「期間は製造が軌道に乗るまで」と言われたことも(笑)。仕事や品質に対する捉え方にもお国柄があります。それを理解した上で、お客さまが求める品質をクリアする方法を実現するには苦労もありましたが、その中で得た経験と知識は私の貴重な財産です。
集大成として「人類の幸せ」に
貢献できるかもしれない
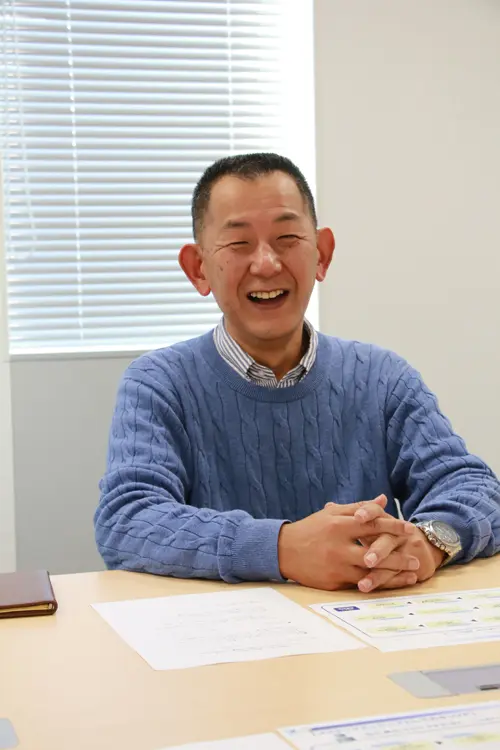
2005年から再び前述の光学機器メーカーへ。今度は家庭やオフィスで使われるインクジェットプリンターの開発です。すでに成熟した製品分野であり、コスト削減、歩留率の向上などを焦点に、確実なアウトプットを13年に渡り心掛けました。2019年からのガラス製品の製造装置の設計と製造管理の仕事では、工場のレイアウトから行います。55歳にして流体解析・構造解析という新しい経験と知識を吸収することができたのが収穫となりました。
そして現在は大手重工メーカーで、次世代エネルギー技術であるアンモニアを燃料とした火力発電の開発チームに参加しています。石炭火力発電削減の一つの解決策とも見なされている技術です。まだ参加したばかりですが、2030年の実用化を目指すプロジェクトの戦力となるべく努力しています。「自分のアウトプットは人類を幸せにしたか?」と自問したとき、自信を持って「はい」と言うのは難しいものです。しかしこの新しい技術がうまくいけば間違いなく多くの人の幸福に結びつく。そう思うと新たな意欲が湧いてくるのを感じます。
エンジニアの仕事は大好きで、これからも可能な限り続けていきたいと考えています。一方で、社会的な活動を行うNPO活動にも興味があります。未来への不確定的要素は数多くありますが、信念と良心を失わず、これからも着実に前に進んでいきます。
(インタビュー:2023年12月16日)